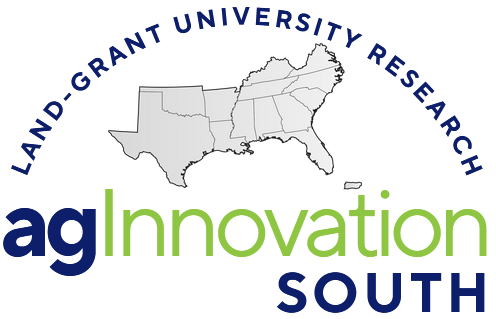
SDC100: New generation advanced fibrous materials from agricultural-based renewable resources and their application in interdisciplinary engineering
(Multistate Research Project)
Status: Inactive/Terminating
Date of Annual Report: 02/21/2019
Report Information
Annual Meeting Dates: 10/28/2018
- 10/28/2018
Period the Report Covers: 10/01/2013 - 09/30/2018
Period the Report Covers: 10/01/2013 - 09/30/2018
Participants
Chunhui XiangYiqi Yang
Srikanth Pilla
Yan Li
Douglas G. Hayes
Andriy.Voronov
Sergiy Minko
Anil N. Netravali
Chen, Jonathan Y"
Suraj Sharma
Patricia A. Annis
Darren Antony Baker
Eric Belasco
You-Lo Hsieh
Brief Summary of Minutes
Accomplishments
<p>Following is the <strong>Termination Report for S-1054</strong> covering the five year project from Oct 1, 2013 to Sep 30, 2018. This report includes Accomplishments and Impacts over the project's five years.</p><br /> <p><strong>S-1054 Termination Report</strong></p><br /> <p><span style="text-decoration: underline;">Project Title:</span> Biobased Fibrous Materials and Cleaner Technologies for a Sustainable and Environmentally Responsible Textile Industry</p><br /> <p><span style="text-decoration: underline;">Duration:</span> 1/1/2013-9/30/2018</p><br /> <p><strong>About the S-1054 Project</strong></p><br /> <p>This multi-state research project addresses the nation’s research priority in bioenergy and biobased products by developing renewable fibrous materials and innovative technologies for eco-friendly and sustainable textile products that have an impact on improving the environment and quality of living. Four research objectives are defined: (1) to develop novel biobased polymeric materials; (2) to develop and evaluate biobased fibrous products for eco-friendly crop protection; (3) to develop and evaluate biobased products for health and safety applications; and (4) to develop and evaluate methods to remove dyes and finishing chemicals from textile waste water. The research progress is made through cooperation among the participants from 11 universities in the states of CA, CO, GA, IA, MS, NE, NY, TN, TX, WA, and WI.</p><br /> <p><strong><span style="text-decoration: underline;">Objective 1:</span></strong> To develop novel biobased polymeric materials (CA, CO, GA, IA, NE, NY, TX)</p><br /> <p><strong><em>CA</em></strong>: At the University of California, Davis, scientists have continued to design and develop sustainable processes to efficiently convert lignocellulosic and protein biopolymers into novel nanomaterials and functional products. Specific progress has been made in novel structure and performance develop of nanocellulose products based on prior accomplishment in isolating cellulose from various agricultural residues and food/beverage by-products and optimizing the derivation of nanocelluloses in varied geometries and surface chemistries. Findings have led to the most extensive understanding of process-linked nanocellulose characteristics from rice straw, the largest agricultural crop residue in the world, and the most diverse range of 1D to 3D nanocelluloses, lignin, and cellulose II nanofibers via electrospinning.</p><br /> <p>Cellulose nanofibrils (CNF)-silica aerogels have been facilely synthesized via a one-step <em>in situ</em> aqueous sol-gel process of polymerizing and aging the silica precursor in the presence of CNFs to encompass the superior dry compressive strength and flexibility of CNF aerogels and the thermal stability of silica aerogels. Sodium silicate (Na<sub>2</sub>SiO<sub>3</sub>) was hydrolyzed and polymerized in the presence of CNFs at varied ratios to synthesize hydrogels whose storage and loss modulus confirmed CNFs to function as the structural skeleton. At the optimal 8:2 CNFs/Na<sub>2</sub>SiO<sub>3</sub> composition, the hydrogels with homogeneously dispersed silica and CNF can be freeze-dried into hierarchically meso-porous aerogels with ultra-low density of 7.7 mg/cm<sup>3</sup>, high specific surface of 342 m<sup>2</sup>/g and pore volume of 0.86 cm<sup>3</sup>/g. This robust sol-gel approach employs naturally abundant silica and cellulose in aqueous system to generate improved CNF-silica aerogels had much higher tensile strength and modulus of up to 177 kPa and 28.5 kPa structural flexibility than silica aerogel and enhanced thermal stability and specific surface over CNF aerogel. Further functionalization of CNF-silica aerogels <em>via</em> organosilane reaction introduced primary amine groups capable of capturing CO<sub>2</sub> with an adsorption capacity of 1.49 mmol/g.</p><br /> <p>Strong and highly conductive aerogels have been assembled from cellulose nanofibrils (CNFs) protonated with conductive poly (3,4-ethylene dioxythiophene)/poly (styrene sulfonate) (PEDOT/PSS) complex at equal mass or less. Protonating CNF surface carboxylates and hydrogen bonding CNF surface carboxyls with PSS in PEDOT/PSS generated PEDOT/PSS/CNF aerogels that were up to ten times stronger while as conductive as neat PEDOT/PSS aerogel, attributed to the transformation of PEDOT benzoid structure to the more electron transfer-preferred quinoid structure. Ethylene glycol (EG) vapor annealing further increased the conductivity of PEDOT/PSS/CNF aerogels by two orders of magnitude. The polydimethylsiloxane (PDMS)-infused conductive PEDOT/PSS/CNF aerogel (70 wt% CNF) transform a resistance-insensitive PDMS-infused PEDOT/PSS aerogel (gauge factor of 1.1×10<sup>-4</sup>) into a stretchable, sensitive and linearly responsive strain sensor (gauge factor of 14.8 at 95% strain).</p><br /> <p>Cellulose fibrous aerogels have been fabricated by a facile and aqueous process that disintegrated electrospun cellulose fibers (ECFs) and reassembled via freezing/freeze-drying with significantly improved dry resiliency and spontaneous 89% shape recovery from ca. 70% compressive strain. Owing to the resilient and 200-300 nm wide ECFs, the cellulose fibrous aerogels exhibited excellent dual dry and wet resiliency as well as improved pore accessibility. The fibrous cellular walls inter-connect the aerogel pore structure to allow extraordinary liquid absorption capacity up to 373 g/g, accounting for 95% of the theoretical absorption capacity. Both highly dry resilient and absorbent properties of the ECF aerogel are highly advantageous for hydrocarbon/oil contamination removal and for hydrocarbon/oil separation applications. In addition, the ECF aerogel could be carbonized into carbon aerogel in supercapacitor for energy storage.</p><br /> <p><strong>Impacts: </strong>Research progress at the University of California, Davis has advanced knowledge on biopolymer utilization from agricultural crop residues and food processing by-products and created new processes, novel functional nanomaterials and performance products. Specifically, cellulose has been efficiently isolated from several major crop residues including rice straw, graph and tomato pomace, cotton linter, and converted to nanocelluloses of nanoscale lateral and up to micro-scale length dimensions and charged or uncharged surfaces. Furthermore, various forms of fibers, films, hydrogels and aerogels have been assembled from these nanocelluloses to exhibit properties potentially useful for separation, catalysis, nanoparticle synthesis and molecular sensing, to name a few.</p><br /> <p><strong><em>CO:</em></strong> PLGA-gentamicin nanoparticles were made using a water-oil method. The nanoparticles were characterized using SEM, TEM, and Nano-Sizer. Molecular acceptors were also synthesized using a typical culture method. The molecular acceptor was grafted to the nanoparticles. The nanoparticles with the acceptor were mixed in a polyethylene oxide solution. The solution was used to develop polyethylene oxide and polyurethane nanofibers via a home-built eletrospinning apparatus. One research grant ($22,000, 2018-2019) was received from the research council of the College of Veterinary Medicine & Biomedical Sciences at Colorado State University. The grant was to support to develop PLGA-gentamicin encapsulated Nanofibers for controlled drug delivery in wound healing. One master student has graduated and completed a thesis entitled “PLGA-gentamicin nanoparticle synthesis”.</p><br /> <p><strong><em>IA:</em></strong> Iowa State University continued on developing biodegradable nanofibers from fermented tea and biobased materials for textiles and composites. The scientists have worked on development of bacterial cellulose nanocomposites from with enhanced mechanical strength by incorporating electrspun poly(lactic acid) (PLA) nanofibers. The resulted bacterial cellulose with PLA nanocomposites showed improved mechanical properties and lower water absorption, which are the key parameters for textile materials used for regular daily wear. One research article was published in a peer-reviewed journal.</p><br /> <p><strong><em>GA</em></strong><strong>: </strong>The University of Georgia (GA) has focused on the development of biothermoplastics from the algal proteins. A study on development of Spirulina microalgae based bioplastics and thermoplastic blends was conducted. A method of thermomechanical process was used to develop bioplastics from Spirulina (blue-green microalgae) and its blends with traditional thermoplastics such as polyolefins. Spirulina biomass was processed into bioplastics by means of plasticization, blending and compatibilization. The extracted protein content and its molecular weight were determined using BCA assay and sodium dodecyl sulfate-polyacrylamide gel electrophoresis (SDS-PAGE), respectively. Thermal, mechanical, and morphological properties of these biobased plastics were tested to assess their performance and possible end-use applications.</p><br /> <p>The adverse effects of non-biodegradable plastic wastes is a growing concern. As an alternative, scientists worldwide are investigating economically viable large scale production of plastics from living resources. Microbial Polyhydroxyalkanoates (PHAs) have attracted research and commercial interests worldwide because they are biodegradable thermoplastic material which are biosynthesized from renewable resources. PHAs are already being produced commercially via bacterial fermentation processes. However, they have to compete economically with petroleum-based polymers. Hence, the development of low-cost production strategies on the basis of diverse renewable materials is a crucial challenge. The use of fewer resources and cost-effective nature of PHAs from photoautotrophic cyanobacteria gives microalgal bioplastics an edge over bacterial fermentation processes.</p><br /> <p>A pilot study of the extraction and characterization of the biosynthesized Polyhydroxybutyrate (PHB) from three oxygenic diazotrophic cyanobacterial species was conducted- Nostoc muscorum, <em>Anabaena variabilis</em> and <em>Anabaena flos aquae</em>. The average intracellular accumulation was 10% (dry cellular weight) with A. flos aquae producing ~26% (dcw). The extracted PHB exhibited comparable mechanical and chemical properties. Based on the cellular adherence and proliferation characteristics of the microalgal PHB, it was found to be a viable substrate in Biomedical-Textile applications such as sutures, prosthetic meshes and woven/knitted bandages for wound healing and scaffolds for tissue engineering. Polyhydroxyalkanoates (PHAs) are a family of linear biodegradable thermoplastic polyesters that are synthesized in nature by bacterial fermentation. The formation is triggered by a deficiency of nutrients and the excessive supply of carbon sources. In spite of the high yield of PHAs via bacterial fermentation, it is not an economically viable route due to high costs incurred by expensive carbon sources and rich oxygen supply during bacterial fermentation. In order to reduce the cost of PHA, photoautotrophic production is thought to be a desired route. Cyanobacteria are one of the only prokaryotic species that naturally produces PHAs (under stress conditions) by photosynthesis and requires fewer resources for growth and biomass production. This research demonstrated that PHA could be produced photoautotrophically and mixotrophically in cyanobacterial species.</p><br /> <p>Fibers that have a diameter under a micron are defined as nanofibers. Electrospinning provides a simple method for the large-scale fabrication of nanofibers. When the diameters of polymer fiber materials are reduced to nano-scale, several unique characteristics such as large surface area to volume ratio, flexibility in surface functionalities, and superior mechanical performance (e.g., stiffness and tensile strength) compared with any other known form of the material. These outstanding properties make the polymer nanofibers to be optimal candidates for many important applications such as filtration, drug delivery systems, battery separators, optoelectronics, sensors, and fuel cells. A core sheath yarn arrangement is defined as a structure made of a separable core constrained to be at the central axis permanently and surrounded by fibers, which act as the sheath. The core yarn serves as a base collector/template for the sheath fibers that cover and coat it uniformly to produce a uniaxial yarn which exhibits high surface area and attractive performance properties. This arrangement shows improved transportation properties (thermal, moisture, liquid, air) compared to the core yarn and has several vital applications in the field of smart and industrial textiles, filtration, tissue engineering, and biomedical devices. Despite the stated advantages, very limited literature is available on the continuous production of integrated electrospun core-sheath nanoyarn production.</p><br /> <p>We prepared a core- sheath yarn arrangement where Poly Lactic Acid (PLA) formed the core yarn and Polyhydroxybutyrate (PHB) nanofibers formed the sheath, which is prepared using electrospinning. The PHB polymers extracted from cyanobacterial species were used in the electrospinning for nano fiber production. The mixotrophic biosynthesis of PHB (poly 3–hydroxy butyrate) in cyanobacteria (blue green algae) (Nostoc sp.) was investigated, and the biosynthesized polymer was extracted using a methanol-chloroform solvent technique. Tested results suggested that the Nostoc sp. culture was a viable candidate for the PHB production and later sheath material for the core-sheat yarn. The resultant core sheath nanospun yarn was characterized for its morphology, thermal properties, biocompatibility and cytotoxicity to determine its use in the biomedical textile applications. The results showed that the incorporation of microalgal Polyhydroxybutyrate in the form of nano- fibrous sheath increased the biocompatibility of the core Polylactic acid yarn due to the improved cell adhesion properties of the yarn.</p><br /> <p><strong>Impacts: </strong>In this research, we studied the potential of microalgae to develop thermoplastic blends and cyanobacterial algae species as an alternative host to replace traditional bacterial process to express biodegradable polyesters, PHAs. The reasons why algae serve as a good candidate for making bioplastics are: less petroleum dependent; the procedure is simple and cost effective for developing value-added biopolymers; algae are of high biomass yield; and simplicity of cultivation, with little impact on the food chain. The exponential intracellular accumulation of PHB in the studied microalgae species in a short period of time indicates the market potential and economic feasibility of the large-scale PHB production for various biomedical applications. This research also explored a nano fibrous arrangement that supported cell growth because of the creation of a sub-micron porous surface. The individual polymeric materials (PHB and PLA) were tested positively for being biosafe and non-toxic material which further bolsters the application of the nano yarn in the biomedical field in the form of sutures, hernia meshes, wound healing gauzes and tissue scaffolds.</p><br /> <p><strong><em>NE</em></strong><strong>: </strong>The team at the University of Nebraska-Lincoln (UNL) includes one research associate professor and one research assistant professor, seven post doc and PhD visiting scholars, 15 graduate students (half PhD, half MS), and 4 undergraduate students from the Department of Textiles, Merchandising & Fashion Design and the Department of Biological Systems Engineering.</p><br /> <p>Textiles affect everyone’s life. The world consumption of fibers is about 100 million metric tons per year. United States are a major consumer of textile products with a total spending of more than 600 billion dollars per year on textile products. As a major pollution creator and consumer of fossil fuels, textile industry has to be changed towards more biobased and more environmentally responsible. We believe our researches will benefit Nebraska from adding values to our agricultural industry and biofuel industry, and from creation of new jobs in the biobased materials industry. Our research is a direct response to the USDA biopreferred program through ‘increasing the purchase and use of renewable, environmentally friendly biobased products while providing "green" jobs and new markets for farmers, manufacturers, and vendors’</p><br /> <p>We focus on developing fibrous materials and biothermoplastics from lignocellulosic agricultural byproducts, from proteins in agricultural coproducts and byproducts, and from synthetic biopolymers for textile and composite applications.</p><br /> <ul><br /> <li><strong>Outputs:</strong></li><br /> </ul><br /> <p>Key outcomes from objective 1 are the successful development of</p><br /> <ul><br /> <li>Protein based biothermoplastic films</li><br /> <li>Biocomposites based on proteins as matrix materials and lignocellulosics as reinforcement</li><br /> <li>Textiles from cotton stalks and cornhusks</li><br /> <li>Continuous production of stereo-complexed PLA fibers and plastics, and</li><br /> <li>Pilot scale wet-spinning of fibers from soyprotein and chicken feather</li><br /> </ul><br /> <ul><br /> <li><strong>Activities:</strong></li><br /> </ul><br /> <p>For Objective 1, what we have done over the past 6 years are:</p><br /> <ul><br /> <li>Steam flash-explosion of plant stocks</li><br /> <li>Extraction of cellulosic fibers from plant stocks with high aspect ratios</li><br /> <li>Chemical grafting of proteins and polysaccharides</li><br /> <li>De-crosslinking and disentangling of highly crosslinked proteins, mainly, feather, wool, camelina and sorghum proteins</li><br /> <li>Dissolution of highly crosslinked proteins with minimum damages to peptides</li><br /> <li>Property characterization of highly crosslinked proteins</li><br /> <li>Thermal behavior of protein and modified proteins such as peanut meals and chicken feathers</li><br /> <li>Stereo complexation and chemical modification of l- and d-polylactides</li><br /> </ul><br /> <ul><br /> <li><strong>Milestones:</strong></li><br /> </ul><br /> <p>Our research resulted in</p><br /> <ul><br /> <li>Thermoplastic films from proteins, distillers grains, meals, and lignocellulosics</li><br /> <li>Fibers from feathers, waste wools, cotton stalks, cornhusks with high aspect ratios, soyprotein and feathers, and</li><br /> <li>Stereo complexed and chemically modified PLA</li><br /> </ul><br /> <p><strong>Impacts:</strong></p><br /> <p>Our researches under Objective 1 were reported and broadcasted. Here are some examples</p><br /> <ul><br /> <li>Our work on producing textiles from agricultural wastes were made into a video called ‘Farm Waste Fashionistas’ for <strong><em>QUEST </em></strong>and aired in many states. They are also reported by medias like <strong><em>Civil Eats</em></strong>, and <strong><em>Nebraska Agriculture and You 2017</em> </strong></li><br /> <li>Our research on bioplastics/polymers was selected to report in the UNL <strong>Year in Review 2017</strong> video, and in Leadership, impacts, challenges: <strong>2017 highlights at Nebraska</strong>. It is also reported by <strong>NIFA Impact Feature, and many news agencies, such as Yale Scientific Magazine </strong>and <strong>Engineering 360 by IEEE.</strong></li><br /> </ul><br /> <p><strong><em>NY</em></strong><strong>:</strong></p><br /> <p><strong><em>Protein based green resins</em></strong></p><br /> <p>A novel, water based, 3-step reaction scheme was developed in this research to obtain thermoset resin from soy flour (SF) without the use of any external crosslinker. SF contains about 55% protein and 32% carbohydrate (sugars) and is the least expensive commercially available soy protein variety. The 1<sup>st</sup> step in this scheme was to separate sugars from protein in the SF. This was accomplished by dissolving sugars while insolubilizing the protein at its isoelectric point and then using a simple lab based filtration technique to separate them. The 2<sup>nd</sup> step consisted of converting the sugar mixture to primarily sugar-aldehyde using a benign water based process. In the 3<sup>rd</sup> step sugar-aldehydes were used to crosslink the reactive amine groups present in the protein separated from SF, mainly utilizing Maillard type reaction. The resulting crosslinked soy protein (thermoset) resin had enhanced mechanical and thermal properties and reduced moisture absorption. This thermoset soy protein resin was used in our later research to produce fully sustainable and biodegradable green nanocomposites by reinforcing it with nano- and micro-fibrillated cellulose (NFC/MFC). This higher strength nanocomposite resin can be further reinforced using other strong cellulosic fibers to form hybrid composites for many applications as replacement for petroleum based conventional plastics and composites. The novel scheme developed in this research may be extended to prepare biobased plastics and composites with enhanced properties by crosslinking other natural proteins as well.</p><br /> <p><strong><em>Self-healing protein based green thermoset resins</em></strong></p><br /> <p>Soy protein isolate (SPI) and other protein based thermoset resins are inherently brittle and easily develop microcracks when put under stress. Once initiated, these microcracks grow with time under continuous stress to form large cracks that can lead to catastrophic failure. The premature failure reduces their useful life significantly. In this research we developed resins based on soy protein isolate (SPI) that can self-heal. Poly(D,L-lactide-<em>co</em>-glycolide) (PLGA) spherical microcapsules (average diameter 778 nm) containing SPI as the healant (SPI-PLGA-MCs) were fabricated using a water-in-oil-in-water emulsification technique. SPI-PLGA-MCs, with different loadings, were uniformly dispersed in the thermoset SPI resin containing glutaraldehyde. When the specimens were tested, SPI-PLGA-MCs in the path of the microcracks were found to fracture and release the SPI (healant). The released SPI was able to bridge the two surfaces of the microcracks and heal them. The results showed that the SPI resin containing 15 wt% SPI-PLGA-MCs and 12 wt% glutaraldehyde had the self-healing efficiency of about 50% after 24 h of healing at RT. The results also confirmed that the SPI released from SPI-PLGA-MCs can easily react with the glutaraldehyde present in the resin as soon as the two come in contact and bridge the two fracture surfaces. The final goal was to show that it is possible to extend the life of green, soy protein based thermoset resin by incorporating self-healing SPI-PLGA microcapsules.</p><br /> <p>Effects of microencapsulation formulation and processing parameters such as PLGA and poly(vinyl alcohol)(PVA) concentrations (1 to 5%) and homogenization speed (1,000 or 10,000 rpm) were investigated to determine their effect on microcapsule size and distribution, protein loading, encapsulation efficiency, morphology of the microcapsules as well as their self-healing efficiency. SPI-PLGA-MCs produced using homogenization speed of 10,000 rpm had an average diameter of 0.76 µm and contained smaller size of sub-capsules within themselves and microcapsules produced using homogenization speed of 1,000 rpm were larger with an average diameter of 9.1 µm and contained diverse size of sub-capsules inside. PVA concentration did not show any significant effect on the SPI-PLGA-MC size. However, higher PVA concentration (5% of SPI-PLGA wt) resulted in aggregation of microcapsules because of the excess PVA residing on the microcapsule surface acted as an adhesive. Excess PVA also resulted in better bonding of SPI-PLGA-MCs to the SPI resin, resulting in higher self-healing efficiency. The self-healing efficiency for various formulations studied varied between 29% and 53%. The SPI-PLGA-MCs prepared using 1% PLGA, 5% PVA and homogenization speed of 10,000 rpm resulted in the highest self-healing efficiency of 53%. This study helped to fine tune the microcapsule preparation process and to engineer the desired size and size distribution of the microcapsules. Future studies will benefit from the results of this study.</p><br /> <p>Our group has also developed self-healing ‘green’ thermoset zein resin using multi-shaped poly(D,L-lactic-co-glycolic acid) (PLGA) microcapsules (MC) containing waxy maize starch (WMS)-based as well as oxidized WMS-based healants. A novel method consisting of co-axial injection combined with emulsion-solvent evaporation technique was developed specifically to fabricate the multi-shaped MCs with aspect ratios larger than 1 and having rougher surface characteristics. While the rougher surface can provide enhanced mechanical bonding between the resin and the MCs, higher aspect ratio increases the probability of MCs being in the path of the microcracks. Both these factors automatically enhance the self-healing efficiency. Our results indicated that WMS and zein do not have strong interactions besides hydrogen bonding. In order to obtain covalent bonding between zein resin and the healant, WMS was oxidized (OWMS) to convert OH groups to aldehyde groups. The aldehyde groups can react with the amine groups in zein to covalently bond them. Self-healing zein resin containing 15 wt% WMS/PLGA MCs, after 24 h of healing at room temperature, showed self-healing efficiency of about 51% in fracture stress. However, in the case of OWMS/PLGA MCs the self-healing efficiency was significantly higher at 72% under identical conditions and same MC loading. Also, at different MC loadings, OWMS performed significantly better than WMS. This significant enhancement is primarily due to the covalent bonding between the zein resin and the OWMS used as healant. This study demonstrated that self-healing thermoset zein resin containing elongated and multi-geometric OWMS-based MCs can be a promising solution to obtain safer and more reliable resins with longer service life. This method can be applied to other protein based resins as well. Such resins can be used in m applications where petroleum-based resins used at present.</p><br /> <p><strong><em>Toughened protein based green thermoset resins</em></strong></p><br /> <p>We have successfully developed another way for toughening SPI based resins by blending natural rubber (NR) or epoxidized natural rubber (ENR) in the form of microparticles. Resin compositions containing up to 30wt% NR or ENR were prepared and their physical, chemical and mechanical properties were fully characterized. While NR did not provide a bonding site, the epoxide groups on the ENR reacted with SPI and covalently bonded them together. This was confirmed using both <sup>1</sup>H-NMR and ATR-FTIR. NR was also seen to phase separate which resulted in SPI/NR resins exhibiting two distinct glass transition temperatures (<em>T</em><em><sub>g</sub></em>) and degradation temperatures (<em>T</em><sub>d</sub>). SPI/ENR resins, on the other hand, showed no separation due to covalent bonding. For SPI/ENR specimens the increase in ENR content from 0 to 30wt% showed major increase in <em>T</em><em><sub>g</sub></em> from -23 to 13°C as a result of cross-linking between SPI and ENR. The increase in ENR content from 0 to 30wt% increased the fracture toughness by about 800% with minimum loss in tensile properties. The results showed that ENR was not only more effective in toughening SPI than NR but the tensile properties of SPI/ENR were also significantly higher than the corresponding compositions of SPI/NR. SPI/ENR green resin with higher toughness could be used as fully biodegradable thermoset resin in many applications including green composites.</p><br /> <p>Yet another novel process to increase the toughness SPI resins has been developed by our group. This 1-step process involves wet electrospinning and blending the ENR fibers directly into SPI resin slurry, prior to crosslinking. ENR electrospinning results showed that as the solution concentration increased from 0.1% to 5%, the surface topography of electrospun ENR fibers (ENRFs) changed from irregular to bumpy. Both topographies provided mechanical bonding with SPI resin. The average diameter of ENRFs also increased from 250 nm to 17 μm with higher concentration. Increased ENRF (electrospun from 3% concentration) loading from 0 to 20% in SPI resin increased the fracture strain significantly from 1.7 to 18.8% and increased the toughness by an order of magnitude. Interestingly, tensile strength and Young’s modulus decreased only slightly compared to the increase in the toughness. Covalent bonding between the epoxy groups in ENR and amine and carboxylic groups in SPI, high aspect ratio of the ENRFs and mechanical bonding, together, contributed to increased toughness of SPI resin while retaining its tensile strength and Young’s modulu</p><br /> <p>We have also been successful in toughening zein-based green thermoset resins. As a comparison, we characterized resins toughened by 3 different methods. These included 1) using traditional plasticizer, sorbitol and the newly developed method using electrospun 2) natural rubber fibers (NRF) and 3) epoxidized natural rubber fibers (ENRF). NRF and ENRF with diameters ranging from sub-micrometer to a few micrometers were electrospun directly into the zein slurry. Chemical, thermal and mechanical properties of zein containing NRF (Zein/NRF) and ENRF (Zein/ENRF) were characterized and compared with those of sorbitol plasticized zein. As in the case of SPI, NRF was immiscible with zein and, as a result, Zein/NRF resins showed two distinct glass transition temperatures (<em>T<sub>g</sub></em>) corresponding to NR and zein. For Zein/ENRF specimens significant increase in both <em>T<sub>g</sub></em> and degradation temperature (<em>T<sub>d</sub></em>) were observed due to crosslinking between zein and ENR. NRF and ENRF were found to be more effective in enhancing fracture toughness of zein than sorbitol. Increased ENRF loading from 0 to 15 wt% showed a significant increase in the toughness value from 0.14 to 5.2 MPa with only minimal decreases in tensile strength and Young’s modulus. Comparably, sorbitol plasticized resin (0.81 MPa) and Zein/NRF resin (0.58 MPa) with same loading showed much less improvement. Crosslinking between ENR and zein is the primary reason for the improvements in properties of the resin, while no such reactions were expected for NR or sorbitol. Zein/ENRF green resin with enhanced toughness could be suitable as environment-friendly thermoset resin in many applications including green composites.</p><br /> <p>This research opens up new possibilities of using fully green and toughened plant protein based resins in many applications such as green composites. The method can also be extended to other plant based green resins such as starches.</p><br /> <p><strong><em>Starch based green thermoset resins</em></strong></p><br /> <p>Starches form another class of inexpensive ‘green’ and biodegradable polymers obtained from plants. In our earlier study, we had crosslinked maize starch for use as resin in composites. However, maize starch is edible. In the new study non-edible mango seed starch (MSS) was extracted from defatted mango seed kernels and crosslinked using a green crosslinker/catalyst system of 1,2,3,4-butane tetracarboxylic acid (BTCA)/sodium propionate (NaP), to obtain thermoset starch resin. Sodium hypophosphite (SHP) has been widely used as a catalyst for esterification of starch or cellulose. However, phosphorous in SHP is toxic to humans and can also pollute underground water table. The results of our study indicated that NaP, a non-phosphorous green catalyst, performs better as a catalyst than SHP. The crosslinking of starch with BTCA/NaP was confirmed using ATR-FTIR spectra and the degree of substitution (DS) values obtained by chemical titrations. Further indirect confirmation of crosslinking was obtained from the increased tensile properties as well as lower swelling of the resin in water. Higher modulus and strength and lower degree of swelling in water using NaP confirmed that NaP acts as a better catalyst than the conventional SHP. Higher crosslinking of starch results in lower moisture absorption which is beneficial and increases its potential application as biobased resin. The crosslinked MSS with strength of about 13 MPa and modulus of about 1.2 GPa is comparable to some petroleum based resins as well as edible starch based resins such as potato or corn starches as well as proteins such as soy protein. MSS would be very inexpensive since most of it is simply discarded as waste.</p><br /> <p><strong><em>Self-healing starch based green thermoset resins</em></strong></p><br /> <p>Starch based thermoset resins are also brittle and develop microcracks when stressed, similar to protein based resins. Based on our study of self-healing protein resins we have successfully developed self-healing waxy maize starch (WMS) based green thermoset resin. This method can be easily applied to all starches. In this case, self-healing was achieved using waxy maize starch-loaded poly(d,l-lactide-co-glycolide) microcapsules (WMS-PLGA-MCs). The WMS resin was crosslinked using 1,2,3,4-butanetetracarboxylic acid (BTCA). A similar water-in-oil-in-water emulsification technique used for proteins was used to obtain WMS-PLGA-MCs. Hydroxyl groups in WMS released from WMS-PLGA-MCs can react with the excess BTCA in the WMS resin and effectively bridge/bond the microcrack surfaces, thus healing the crack. In this case the highest self-healing efficiency in fracture stress of up to 51% was achieved by dispersing 20% WMS-PLGA-MCs by weight, after 24 h of healing at RT. In the case of fracture toughness the self-healing was even higher at about 66%. Self-healing starch-based resin developed in this study is not only green and fully sustainable but the fabrication processes including microencapsulation preparation are water-based and can be easily scaled up.</p><br /> <p>The nontoxic starch based green resin can be useful for fabricating green composites in many indoor applications such as automotive, aerospace, housing and packaging, as replacement for currently used petroleum based composites.</p><br /> <p><strong><em>TX</em></strong><strong>: </strong>Research has been done on an approach for use of waste polyethylene terephthalate (PET) and waste paper to synthesize unsaturated polyester resin (UPR). Via depolymerization, recycled PET was converted into oligo-polyethylene terephthalate (OPET) and recycled paper was transformed into oligo-cellulose (OC). UPR was produced by a reaction of the OPET and OC with maleic anhydride (MA). Polymer characterization of UPR and glycolytic PET and cellulose was carried out in terms of molecular weight, crystalline structure, functional groups, thermal stability, and specific organic compound identification. The research revealed that degradation of the cellulose occurred in the amorphous region, resulting in an increase of crystallinity index for OC. This indicated that oligomers with smaller glucose chains were obtained by a hydroxyl substitution reaction. Characterized data confirmed that OC had an enhanced hydrophobicity and thermal stability because of esterification. Resulted UPR also showed an improved crystallinity and higher thermal stability.</p><br /> <p><strong>Impact: </strong>This research aims at developing a synthesizing method to produce unsaturated polyester resin (UPR) from waste paper and waste PET. Resulted UPR features improved biodegradability and increased polymer crystallinity. Feasibility of this approach could help recycle PET and cellulose. As a result, the research would bring a benefit for reduction of solid waste materials and enhancement of environmental protection.</p><br /> <p><span style="text-decoration: underline;"><strong>Objective 2</strong>:</span> Biodegradable Green Composites from Food and Agricultural Processing Wastes</p><br /> <p><strong><em>NY</em></strong>:</p><br /> <p><strong><em>Self-healing</em></strong> <strong><em>protein based green composites</em></strong></p><br /> <p>The success of the development of self-healing soy protein based resins has been extended by our group to fabricate self-healing soy protein-microfibrillated cellulose (MFC) reinforced (MFC-SPI) green composites. In this case we used a green solvent (ethyl acetate) based process to produce SPI-PLGA-MCs. The new process resulted in high protein loading of over 50%. Self-healing MFC-SPI composites with uniformly dispersed MFC (10wt%) and 15wt% of SPI containing PLGA microcapsules (SPI-PLGA-MCs), resulted in fracture stress of 15.2 MPa and Young’s modulus of about 1 GPa and SPI composites with only 10wt% of MFC (no microcapsules) showed higher Young’s modulus of 1.4 GPa and fracture stress of 24.5 MPa. Both these properties were significantly higher compared to pure SPI resin due to the inherently high aspect ratio and tensile properties of MFC as well as its excellent hydrogen bonding ability with SPI resin due to the presence of polar groups in both. Self-healing i.e., bridging of fracture surfaces of the microcracks by the released SPI (healing agent), was confirmed through SEM imaging as well as tensile properties after healing. Composites with no SPI-PLGA-MCs showed no self-healing as was expected. However, self-healing SPI composites showed self-healing efficiency of 27% after 24 h of healing. The 27% self-healing efficiency observed for composites is much lower compared to that of pure resin (over 50%). This is simply because in composites only the resin has the ability to heal. Microfibrils which are the reinforcing component, once broken cannot heal. As a result, only lower self-healing efficiency can be expected.</p><br /> <p><strong><em>Self-healing thermoset</em></strong> <strong><em>starch based green composites</em></strong></p><br /> <p>Green composites were developed using waxy maize starch (WMS) resin and micro- and nano-fibrillated cellulose (MFC/NFC). Further, an environmentally friendly, sustainable, and water-soluble crosslinker, 1,2,3,4-butanetetracarboxylic acid (BTCA), was used to crosslink WMS to fabricate crosslinked starch-based composites. This provides a benign and convenient method to produce crosslinked thermoset starch-based composite films, comparable to commercially available plastic sheets. The process can be easily scaled up for commercial production. In this work industrially pregelatinized WMS was used to obtain smooth, transparent and defect-free films. Crosslinking not only improved the mechanical properties of the films but also helped to reduce their moisture absorption and made both resin and composites insoluble in water. Crosslinked WMS composite films containing 15% MFC exhibited excellent tensile properties with a Young’s modulus of over 2.3 GPa and fracture stress of 39 MPa. This was clearly a result of the MFC/NFC incorporation which has excellent tensile properties. The toughness of these composites was also significantly higher, even without the use of any plasticizers such as glycerol or sorbitol. This was a result of the crack bridging ability of the MFC/NFC which have very high aspect ratio. These materials can be good candidates for replacing petroleum-based resins such as epoxies and their composites.</p><br /> <p>We have also fabricated green composites based on non-edible starch-based resin, which is often wasted, and micro-fibrillated cellulose (MFC). Earlier it was mentioned that starch was extracted from mango seed kernels (MSS), a waste source freely available in tropical regions, and thermoset resin was prepared. MFC was used to reinforce MSS based resin in order to take advantage of the chemical similarity between the starch and the MFC cellulose which results in good interfacial bonding. Uniform dispersion of MFC in starch was obtained using homogenizer. In this case as well the crosslinking was achieved using BTCA, an environment friendly crosslinker. Confirmation of crosslinking was obtained from ATR-FTIR spectra. MFC/MSS green composites, in sheet form, were prepared by solution casting method. Tensile and thermal properties of MFC/MSS green composites were comparable to the edible starch-based composites and can be expected to perform similarly. The thermoset resins obtained from mango seed kernel can replace currently available resins derived from the edible sources as well as petroleum-based resins for packaging, coatings, mulches and other applications.</p><br /> <p><strong><em>Protein based ‘Fire Resistant’ green composites</em></strong></p><br /> <p>Proteins contain significant amount of nitrogen which makes them inherently fire retardant. Soy protein is also considered to be naturally fire resistant compared to many conventional polymers. We have characterized the fire performance of green composites made using jute fabric and soy protein concentrate (SPC). The SPC resin also contained halloysite nanotubes (HNT), naturally occurring aluminosilicate clay in rolled up form, which can enhance resin stiffness as well as fire retardancy. The results revealed that both Young’s modulus and tensile strength of neat resin increased and fracture strain of neat resin decreased with HNT loading. Tensile properties of the green composites were not affected by HNT addition but depended on the jute fabric properties. Most importantly, the results suggested that SPC resin has lower flammability (heat release capacity) than some of the conventional resins derived from petroleum such as vinyl esters and epoxies. Results also confirmed the hypothesis that up to 5% loading of HNT had a positive impact on reducing the flammability, while the mechanical properties were not affected. These results are significant and suggest that soy protein based resins may be used for housing and other civil structures where reduced flammability may be very desirable.</p><br /> <p><strong><em>Corrugated paper-</em></strong><strong><em>starch based green composites</em></strong></p><br /> <p>Corrugated composites were developed by using starch based emulsion-type biodegradable resin and newspaper print. While starch is plant-based and fully renewable, newspaper print is also produced from sustainable wood pulp. Once used for just one day, some of the newspaper is collected but may not be used effectively. Composites offers a way to up-cycle the used newsprint in value-added applications. These composites have excellent mechanical properties and can be used in many applications including durable and strong boxes/cartons for shipping or even panels for office cubicles. Thus the composites provide a high value-added outlet for the agriculture and food wastes. One of the greatest advantages of these green composites is that the entire composites can be composted after their intended life to create organic soil, completing the nature’s intended carbon cycle.</p><br /> <p><span style="text-decoration: underline;"><strong>Objective 3</strong>:</span> Advanced Green Composites from Food and Agricultural Processing Wastes</p><br /> <p><strong><em>CA:</em></strong> Research conducted at the University of California, Davis, has demonstrated cellulose microfibers to be effective templates to immobilize bacteriophages to broaden their applications in targeting bacterial pathogens in foods and medicine. This study evaluated physical adsorption, protein-ligand binding and electrostatic interactions bound mechanisms so not to chemically nor genetically modifying the phages to enable effective translation of naturally occurring phages and their cocktails for antimicrobial applications. The immobilization approaches were characterized by phage loading efficiency, phage distribution, and phage release from fibers. Overall, the electrostatic immobilization approach bound more active phages than physical adsorption and protein-ligand binding and thus may be considered the optimal approach to immobilizing phages onto biomaterial surfaces.</p><br /> <p><strong><em>MS</em></strong><strong>:</strong> In addition to adding high value to agricultural byproducts and coproducts, textile materials can help to protect the citizens, agricultural commodities and infrastructure from internal and external biological threats. As part of this research, high-performance textiles will be developed that defend public and healthcare personnel from biological hazards, as well as protect fire fighters and first responders from fire hazards. This part of the project will address three key focus areas as identified by The National Strategy for Homeland Security: 1) defending against catastrophic threats (bio-defense); 2) protecting critical public health and safety infrastructures; and 3) domestic counter-terrorism. In addition, this research will study the ability of textile materials to provide protection against healthcare associated infections (HAI) which have recently emerged as a major concern among health care professionals (Vigo, 2001; Liu, 2001). </p><br /> <p>Protecting farms and enhancing productivity are vital to the economic competitiveness and sustainability of our agricultural crops that is related to the Science Roadmap for Agriculture prepared by the National Association of State Universities and Land-Grant Colleges (NASULGC) and Experiment Station Committee on Organization and Policy (ESCOP). The biodegradable mulches that will be developed in this project will help to protect crops, reduce costs and decrease environmental pollution and achieve the goals set by NASULGC. The work on development and evaluation of eco-friendly meshes for insect control will reduce the use of chemical pesticides and shed light on alternative methods of pest management in our farms. </p><br /> <p>As Earths population increases, there has been tremendous increase in the demand of fresh water for farming, food preparation and processing, textile production, and daily use, etc. The cost of managing, treating, and delivering fresh water is rising very rapidly. The green seed coatings will provide not only the boost to initial growth but protection from fungal attack The textile industry is a major consumer of fresh water. Ecotextile News reported in the 2009 April issue that, globally, approximately 1.2 billion cubic meters of water are used annually for cleaning and bleaching of textiles alone. Much more is used in dyeing, finishing and other textile processes. In addition, more than 2.4 billion lbs of dyes, detergents and auxiliary chemicals were used by world textile industries. However, current methods of continual purification of the wastewater has shown build ups of different contaminations and poor dyeing finishing performances. Conventional filtration, followed by acid base neutralization, has been used with very limited success. Electrochemical oxidation (Vlyssides, 1998) and ozonation (Ehud, 2006) are examples of newer technologies. Recently, a new photochemical and photo catalytic oxidation (PECO) technology has been developed at UW-Madison to convert aqueous ammonia into nitrogen gas (Ramsey, 2009). The potential application of this new technology to treat textile waste water will be studied as part of this proposed research.</p><br /> <p><strong><em>NE</em></strong>: Our main focuses are on developing protein based fibrous matrices as tissue engineering scaffolds and hollow nano particles as drug delivery vehicles.</p><br /> <p><strong>Accomplishments:</strong></p><br /> <ul><br /> <li><strong>Outputs:</strong></li><br /> </ul><br /> <p>Key outcomes from objective 3 are the successful development of</p><br /> <ul><br /> <li>A New electrospinning technology for production of 3D fibrous materials</li><br /> <li>Tissue engineering scaffolds with excellent performance properties from plant proteins, collagen and feathers</li><br /> <li>Protein nanoparticles for effective drug delivery to spleen, liver and kidney, and</li><br /> <li>Green and safe hair perming and straightening technologies</li><br /> </ul><br /> <ul><br /> <li><strong>Activities:</strong></li><br /> </ul><br /> <p>For Objective 3, what we have done over the last 5 years are:</p><br /> <ul><br /> <ul><br /> <li>Developing new electrospinning technology for biopolymers</li><br /> <li>Formation of collagen, keratin, camellia and sorghum protein fiber for tissue engineering applications</li><br /> <li>Decrosslinking and recrosslinking of proteins, and</li><br /> <li>Fabricating hollow protein nanoparticles</li><br /> </ul><br /> </ul><br /> <ul><br /> <li><strong>Milestones:</strong></li><br /> </ul><br /> <p>Our research resulted in</p><br /> <ul><br /> <li>New method of 3D electrospinning of randomly oriented fibers</li><br /> <li>Water stable collagen nanofibers as tissue engineering scaffolds</li><br /> <li>Water stable tissue engineering scaffolds from highly crosslinked proteins: Keratin, camellia and sorghum</li><br /> <li>Stable nanoparticles from zein and keratin with controlled degradability and delivery, and</li><br /> <li>Human hair manipulations</li><br /> </ul><br /> <p><strong>Impacts: </strong>Our research on hollow protein nanoparticles as drug delivery vehicles was reported by the Office of Research & Economic Development of UNL in the <strong>Research Annual Report 2014-2015, titled “Protecting Nanoparticles Carrying Therapeutic Drugs”, and </strong>Our research on collage fiber scaffolds and the crosslinking system was reported as a cover story by <strong>Journal of Biomedical Materials Research Part A</strong></p><br /> <p><strong><em>NY</em></strong>: Green composites made using natural fibers such as jute, kenaf, etc., have moderate strength and stiffness comparable to wood and wood-based products such as plywood, particle board or medium density fiber boards. As a result, they can be used as replacement of wood or wood based products in many applications. One of our goals were to make very strong and tough composites that may one day replace aramid fiber (e.g. Kevlar<sup>®</sup>) based composites that are used for ballistic protections. We utilized liquid crystalline cellulose (LCC) fibers which have strength in the range of about 1600 MPa and fracture strain between 5-10%. In the present case the fibers were treated with KOH solution to improve their mechanical properties. Treated fibers were used to fabricate unidirectional composites using soy protein based resin. The KOH treatment increased the fiber strength significantly. This improved strength was also transferred to the composite properties. With 65% fiber volume, it should be possible to obtain composite strength of about 1 GPa, making them truly advanced green composites. Their toughness was also high and can replace composites currently used in ballistic applications.</p><br /> <p>We have also used thermal and mechanical treatments in combination with the chemical treatment to enhance the strength of the LCC fibers close to 2 GPa. In theory, composites made using these fibers, at 65% volume content, can have strength over 1.2 GPa. Such advanced green composites can be used in structural applications.</p><br /> <p><strong>Impact: </strong>Our research is directly related to the nation’s efforts in reducing the wastes from agricultural and food processing by utilizing them to create value-added, fully renewable and biodegradable ‘green’ materials. Unlike the current petroleum based resins and composites which mostly end up in landfills, high performance green resins and composites developed in this project can be easily composted or disposed of without harming the nature. In fact, composting creates organic soil that can be used for growing plants. Using green resins/composites to replace currently available petroleum based polymers and composites would support the Government’s ‘Bio-preferred’ program. There are other significant advantages as well. For example, using wastes prevents contamination of land and water. It also saves wastes from entering the nation’s already-overloaded landfill system. Creating value for the agricultural wastes can also help the farmers by increasing their income.</p><br /> <p>In our research we have clearly demonstrated that the useful life of soy protein based resin can be increased 1) by using SPI filled PLGA microcapsules to achieve self-healing and 2) by toughening the resins by adding electrospun natural rubber (ENR) nanofibers in a simple and scalable 1-step process. Similarly, starch based resins can be toughened or given self-healing characteristics. Such resins can have much longer service life making them economical. They are also safer.</p><br /> <p>Microfibrillated and nanofibrillated cellulose (MFC/NFC) reinforced SPI resin based green composites were also prepared. While MFC/NFC from kraft paper pulp was used in the current studies, it can be obtained from various waste sources and by-products such as apple pulp, orange pulp, carrot pulp, grape pomace and many others. Further, these reinforced resins could be used as resins to fabricate unidirectional composites using high strength continuous fibers. Our research group has successfully fabricated self-healing green composites as well. Self-healing characteristic can extend their durability and make it easier for them to compete with conventional composites derived from petroleum. We have successfully toughened SPI and starch based resins, which are inherently brittle, using epoxidized natural rubber. These green resins with higher toughness could be easily used as fully biodegradable thermoset resin in many applications including green composites. This research opens up new possibilities of using fully green and toughened SPI resins in many applications including green composites.</p><br /> <p>The self-healing technique has been further extended to obtain starch based resins that self-heal and provide significant benefits. Similarly the simple 1-step process developed for blending electrospun fibers for soy protein based resin toughening can also be extended to other protein and starch based resins. We have also used waste sources for obtaining starch for resin. For example, starch was extracted from mango seed kernel and crosslinked to form thermoset resin. Further, this resin was used to fabricate green composites using MFC as reinforcement. The properties of these composites were comparable to soy protein based composites.</p><br /> <p>Although the liquid crystalline cellulose fibers were developed and produced in Europe, the technology is currently being developed in the US. For example, within this program (S-1054), medium strength cellulose fibers which can be used in textile applications have already been developed. With increased molecular orientation and higher crystallinity, properties of these fibers can be increased significantly and made suitable for high strength applications including composites. The advanced green composites with high strengths and toughness may also be used in ballistic applications.</p><br /> <p><span style="text-decoration: underline;"><strong>Objective 4</strong>:</span> to develop and evaluate methods to remove dyes and finishing chemicals from textile waste water.</p><br /> <p><strong><em>GA</em></strong><strong>:</strong></p><br /> <p><strong>Accomplishments Report for Nanocellulose based dyeing/coating technology</strong></p><br /> <p><strong>Outcomes:</strong> The first price ($57,000) for the Sustainable Textile Dyeing Using Nanocellulosic Fibers Project was received by the UGA team at Green & Sustainable Chemistry Challenge by ELSEVIER. The price was used to hire a postdoc for the research continuation. </p><br /> <table><br /> <tbody><br /> <tr><br /> <td width="618"><br /> <p><strong>Green and Efficient Textile Dyeing and Finishing Technology Using Nanocellulosic Fibers - Co-fund </strong>Cotton Research and Development Corporation, <em>January 1, 2018–December 31, 2018</em>. Amount: $ 29,855 (US)</p><br /> </td><br /> </tr><br /> <tr><br /> <td width="618"><br /> <p><strong>Green and Efficient Textile Dyeing and Finishing Technology Using Nanocellulosic Fibers</strong> COTTON INCORPORATED, <em>January 1, 2018–December 31, 2018</em>. Amount: $ 29,855 (US)</p><br /> </td><br /> </tr><br /> </tbody><br /> </table><br /> <p><strong>Outputs:</strong> Conference presentations, patent application, workshop presentations for industrial partners.</p><br /> <p><strong>Activities:</strong> Nanocellulose (NC) hydrogel textile dyeing and finishing technology has been developed and tested at the laboratory scale. We have studied the mechanisms of the functionalization of textiles using NC fibers as a functional coating material. The mechanisms involve incorporation of functional molecules/particles in individual and networked NC fibrils, followed by the subsequent anchoring of the NC network to the textile surfaces via hydrogen/covalent bonds, crosslinking, and physical entrapment/entanglement. As a proof of concept of the use of NC as functional coating materials for textiles, we show that NC fibers labeled with reactive dye molecules are anchored to the surfaces of natural/synthetic fibers and the coatings demonstrate noticeable durability.</p><br /> <p><strong>Milestones:</strong></p><br /> <ul><br /> <li>Development NC-bases textile dying technology 2016-2017</li><br /> <li>Testing of technology for different type of reactive dyes 2018</li><br /> <li>Application of NC crosslinking for improved dye fixation of the textile coatings 2018</li><br /> </ul><br /> <p><strong>Impacts: </strong>The benefits of the developed technology are in e<em>nvironmental sustainability, improved performance,</em> and the <em>reduction of manufacturing costs</em> of producing colored and functional fabrics. The key advantages of using NC materials to bind dyes, pigments and finishing chemicals to cellulosic and other fibers are the greatly reduced use of water and improved manufacturing logistic. This will be implemented in the traditional dyeing process through elimination of multiple rinses typically used in the conventional dyeing and unlimited recycling of the dyeing solutions owing to NC long-lasting dyeing potency. The unparalleled potential of the proposed technology will be used for coloration with reactive dyes and pigments when the coloration process could be compatible with padding, printing, spraying, etc. and applied to different types of blended textiles using the same NC-platform. It is worth recalling that NC-gels can be produced from cellulosic wastes that is normally not used in an industrial setting. The first price ($57,000) for the Sustainable Textile Dyeing Using Nanocellulosic Fibers Project was received by the UGA team at Green & Sustainable Chemistry Challenge by ELSEVIER.</p><br /> <p><strong><em>NE</em></strong>: Our main focuses are on technology for process and chemical replacement, and effluent reduction, although we also worked on waste removal from the end of the pipeline.</p><br /> <p><strong>Accomplishments:</strong></p><br /> <ul><br /> <li><strong>Outputs:</strong></li><br /> </ul><br /> <p>Key outcomes from objective 4 are the successful development of</p><br /> <ul><br /> <li>Completely biodegradable sizes to replace PVA, the major pollutant in textile wastewater</li><br /> <li>A new method for high efficient and low cost removal of dyes, chemicals and organic solvents in spent dyebath and textile wastewater using biofibers from freeze-extruded biofiber matrices</li><br /> <li>Waterless dyeing systems to minimize/eliminate salt, dye and chemicals in spent dyebath for polyesters and cellulosics</li><br /> <li>Green crosslinking systems from polycarboxylic acids and oxidized saccharides</li><br /> <li>Hydrolysis-free dyeing system for PLA, and</li><br /> <li>Dyeing of wool with colorants from sorghum hull</li><br /> </ul><br /> <ul><br /> <li><strong>Activities:</strong></li><br /> </ul><br /> <p>Our major activities under Objective 4 are:</p><br /> <ul><br /> <li>Characterization, purification and manipulation of plant proteins, meals, feathers and distillers grains</li><br /> <li>Formation and improvement of films from plant proteins, meals, feathers and distillers grains</li><br /> <li>Fabrication and characterization of nanoparticles from zein, and keratin</li><br /> <li>Formation of 3D interconnected fibrous matrix using freezer dryer</li><br /> <li>Crosslinking of cellulosics and proteins using polycarboxylic acids and oxidized saccharides</li><br /> <li>Color extraction from sorghum hulls, and</li><br /> <li>Waterless dyeing</li><br /> </ul><br /> <ul><br /> <li><strong>Milestones:</strong></li><br /> </ul><br /> <p>Our research resulted in</p><br /> <ul><br /> <li>Textile size from plant proteins, feathers and distillers grains to substitute PVA</li><br /> <li>Successful industrial scale demonstration of effective high speed weaving using sizes from soyproteins</li><br /> <li>Dye sorbent from hollow protein nanoparticles</li><br /> <li>Improved mechanical properties and water resistance of products from proteins and polysaccharides</li><br /> <li>Dyes from sorghum hulls</li><br /> <li>A new fiber extrusion method: Freeze-extrusion</li><br /> <li>Technology of waterless dyeing of Cotton and PLA</li><br /> </ul><br /> <p><strong>Impacts: </strong>Our research on Green crosslinking system was reported by <strong>ACS (American Chemical Society) News Service Weekly PressPac.</strong> Our research on Sustainable and Hydrolysis-Free Dyeing Process for Polylactic Acid was reported as the cover story by<strong> ACS Sustainable Chemistry & Engineering, </strong>and was selected by the editor of the journal to be included in<strong> the Virtual Special Issue on Promoting the Development and Use of Quantitative Sustainability Metrics.</strong> Our research on colorants from sorghum hull for wool dyeing was reported by <strong>USDA in NIFA Update, ACS News Service Weekly PressPac, the Science Times, </strong>and many other agents.</p><br /> <p> </p>Publications
Impact Statements
- See Termination Report under Accomplishments section.