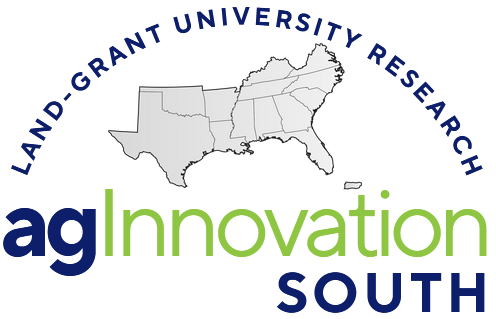
SDC303: Production, Harvest, Storage, and Delivery of Herbaceous Energy Crops for Fuel and Chemicals
(Multistate Research Project)
Status: Inactive/Terminating
SDC303: Production, Harvest, Storage, and Delivery of Herbaceous Energy Crops for Fuel and Chemicals
Duration: 06/01/2003 to 05/30/2008
Administrative Advisor(s):
NIFA Reps:
Non-Technical Summary
Statement of Issues and Justification
Use of renewable energy resources to meet society's needs reduces the release of fossilized carbon into the atmosphere, provides new markets for agriculture, and reduces the balance-of-payment problem caused by importation of over 50% of the petroleum required by the U.S. economy. The U.S. has not signed the Kyoto Treaty and thus agreed to voluntarily reduce CO2 emission. Since the U.S. economy consumes 20% of the world?s fossil fuel energy, the decision to continue current policies places the U.S. in an unfavorable light in the world community. In August 1999, President Clinton did sign Executive Order 13134 and Memorandum on Promoting Biobased Products and Bioenergy, aimed at tripling U.S. use of biobased products and bioenergy by 2010. Energy prices are dominated by petroleum prices. Since the oil shortages of the 1970s, plans for alternate energy have advanced and retreated with petroleum prices. When petroleum prices rise, interest in alternate energy increases. Americans, because of their infatuation with transportation, particularly automobiles, are very sensitive to political decisions that affect fuel prices. For this reason, the U.S. government has been reluctant to adopt a long-range policy to protect the environment by producing more energy from renewable resources. If such a policy was implemented, for example, if a goal was set to produce 20% of our energy from renewable resources by the year 2020, energy prices would rise until this goal was met. The market will work to meet the goal in the most efficient way possible. One of the goals of this research is to provide estimates of renewable energy feedstock delivered cost based on real data from existing agricultural industries that are similar to an envisioned energy-from-herbaceous-biomass industry. Even though current energy prices do not suggest that biomass can compete with fossil fuels, the current volatile world political scene suggests that studies must continue to show how biomass resources, defined as processing wastes and energy crops, can be efficiently collected, stored, and delivered to a conversion facility. Combustion of fossil fuels releases millions of tones of carbon into the atmosphere. This newly added CO2 will remain from decades to thousands of years. There is legitimate concern that the release of this carbon is causing, and will cause, global climate change. When biomass is used for fuel, the carbon cycle is closed; the released CO2 is captured by the plants growing to replace the biomass being burned. This proposal focuses on herbaceous material resulting from an annual harvest of agricultural fields; thus, it is a longer-term effort. It is expected that several species of perennial grasses will be grown in a production area surrounding a conversion plant. These stands will be managed to provide a range of harvest dates over a 9-month period, May - January, with the winter harvest being grass that has dried standing in the field.
Related, Current and Previous Work
Objectives
-
Develop strategies for management of different species of herbaceous biomass crops such that harvesting can be done from mid May to the end of January (delayed harvest of dry standing biomass), a 34-week harvest season.
-
Develop harvesting and in-field hauling procedures to minimize the cost of these two operations using the round baler and a self-propelled, self-loading round bale hauler.
-
Use the logistics data from existing industries (cotton and/or sugar cane) for a systems analysis study to define the equipment and management strategy needed to optimize the productivity of over-the-road hauling of herbaceous biomass from on-farm storage sites to a central conversion plant.
-
Design, build, and field test new equipment needed for an herbaceous biomass industry.
-
Use the various operating parameters defined by objectives 1 - 4 to conduct a system analysis, which compares the various options for harvest, storage, and delivery of biomass to a central conversion plant.
-
Methods
Objective 1. Two agronomists, one from the lower southeast and one from the upper southeast, will join with engineers from four states to accomplish Objective 1. There are key systems issues relative to mix of species planted in the production area and management of these stands as to harvest frequency (1, 2, or more cuts per year) and potential for delayed harvest during winter months. Objective 2. Plans are to develop a sensor/procedure to measure mass flow into a round baler. The mass flow sensor will be interfaced with the shift control program on the tractor to adjust forward speed and thus the flow of hay into the baler. Technical support from a tractor manufacturer (CNH or Deere) is envisioned. Objective 3. Logistics studies are underway to optimize the transport of cotton modules to a gin. Knowledge gained is expected to be directly transferable to the analysis of a production area with given on-farm storage locations, road network, and biomass conversion plant location. Objective 4. Round bales can be stored in ambient on-farm locations. These bales can be transported at a reasonable cost, if a means can be developed to quickly load and unload trucks. A special frame is required to haul a 28-bale load. Engineers in one state will work on the frame design and engineers in another state will design the loader to load round bales into the frame. The key is the development of procedures to load and unload quickly (minutes) so that an individual truck can haul as many loads per day as possible. Increasing tons-per-day-per-truck reduces $/ton hauling cost. Objective 5. It is expected that individual contributions from participants (scientists, engineers, and economists) will be combined to simulate feedstock delivery to several hypothesized central plants, ideally, one in each participating state. The systems analysis will calculate the average annual cost of feedstock ($/dry Mg) for assumed production areas: 1. 20-mi radius with 60% of available field diverted to biomass. 2. 40-mi radius with 50% of available fields diverted to biomass. 3. 40-mi radius with 30% of available fields diverted to biomass.Measurement of Progress and Results
Outputs
- This project will develop the methodoly needed for planning and operating the production, harvest, storage, and delivery system required to deliver feedstock from 20,000 acres of cropland to a central conversion plant. As time and funding permits, this methodology will be applied to one multi-county production area in each participating state. At some point, the decision will be made to produce x percentage of liquid fuel from renewable resources by y year. The states with planning already done will be the first states to get conversion plants sited by the major energy companies.
- Round bales can be stored in ambient on-farm storage. Once a square bale is rained on, there is no way to get it dry again. The round bale, because it sheds water and protects itself, is the obvious choice for the Southeast. The key to making a round bale system work is the development of technology to load and unload round bales onto trucks.
- The sugar cane industry and the cotton industry both have efficient trucking systems to collect large quantities of herbaceous biomass at a central plant. Both industries have found ways to quickly load and unload so individual trucks can haul more tons per day. This project will define the equipment needed to load and unload round bales and develop the management procedures to use this equipment efficiently.
- Round balers typically operate at about 65% of rated mass input. If this mass flow can be measured and tractor speed controlled to achieve 90% of rated input, per-ton baling cost will be reduced. This project will develop a mass flow sensor and integrate this measurement with tractor control to increase baler productivity.